I costi nascosti dell’Aria Compressa:
come IDA ha identificato un margine di efficientamento del 70%
Quando le macchine sono spente, l’aria compressa dovrebbe costare zero. Un’azienda manifatturiera ha invece scoperto perdite per 53.000€ l’anno. La storia di come il monitoraggio digitale ha svelato e risolto questo spreco invisibile.
Efficienza industriale: le storie che nessuno racconta
Come si traducono i vantaggi generati da IDA nel gergo aziendale? Oggi diamo inizio alla rubrica “la voce dell’esperto”, perché chi meglio della voce del nostro comparto tecnico è in grado di svelare tutto il potenziale dell’applicazione creata in Maxfone?
Attraverso l’analisi di situazioni critiche, tra le più interessanti di questi ultimi anni, l’area tecnica della Data Factory ci racconta in che modo IDA contribuisce a risolvere le sfide giornaliere che affrontano le PMI, migliorando le loro performance e fornendo un notevole contributo al loro efficientamento in termini di costi ed energia utilizzata. Ad inaugurare questa nuova rubrica ci pensa l’aria compressa. Imprenditori e imprenditrici, vi siete mai chiesti quanto incide il consumo di aria compressa sui costi aziendali? Ve lo svela il nostro esperto!
La lunga e spesso articolata filiera delle produzioni italiane richiede un accurato studio e una preparazione strategica da parte delle aziende che, prima di arrivare al prodotto finale, devono fare i conti con numerosi fattori, tra questi la gestione delle risorse e i consumi energetici. Ma non solo!
I processi produttivi richiedono impegno e lavoro di squadra. È facile ricercare e pianificare soluzioni a tavolino, in grado di fornire in via teorica la prassi per risolvere un problema o per superare un ostacolo durante i processi produttivi. Ma cosa succede se nel pratico tali proposte non trovano riscontro positivo? Il rischio è un dispendioso impiego di energie, tempo e denaro per soluzioni poco concrete e poco convenienti.
Se per il lavoro di squadra ci pensano le pratiche di formazione e di team building da adottare periodicamente, decidendo tempi e modalità all’interno dell’azienda stessa; per il monitoraggio efficiente dei processi produttivi ci si affida spesso a soluzioni e a consulenti esterni.
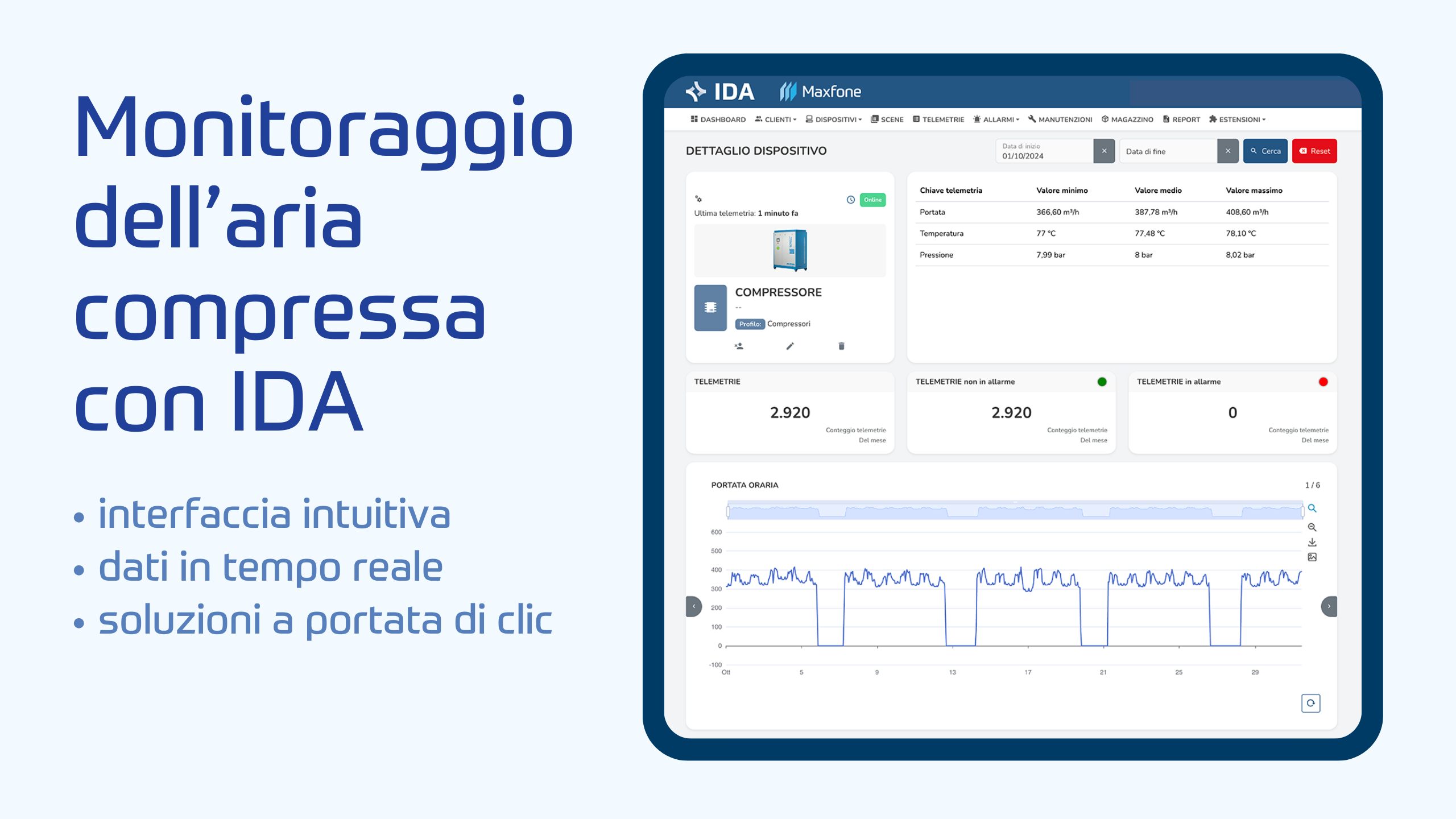
La criticità di partenza
Oggi le esigenze dell’industria manifatturiera convergono verso la ricerca di soluzioni più sostenibili in grado di impattare il meno possibile sull’ambiente e sul territorio circostante. Le PMI si affidano sempre di più all’innovazione digitale per usufruire di soluzioni accurate capaci di tenere sotto controllo costi e consumi in ottica responsabile.
Sempre più aziende si affidano a IDA per monitorare i propri parametri di produzione, dal consumo elettrico fino a metriche avanzate, come l’emissione di CO₂ equivalente e l’impronta idrica. Tuttavia, c’è un consumo che incide in maniera sostanziosa sulle tasche di un’azienda produttiva e che spesso viene ignorato: stiamo parlando dell’aria compressa. L’aria compressa è una delle quattro principali utilities del settore industriale insieme ad energia elettrica, gas e acqua, la cui disponibilità e funzionamento viene data per scontato.
A differenza delle altre utilities, il cui costo viene periodicamente tracciato tramite le bollette, l’aria compressa risulta più complessa da misurare, e il suo impatto economico è conseguentemente nascosto, contabilizzato come parte del consumo elettrico totale dell’impresa.
Questo problema è facilmente risolvibile tramite l’applicazione IDA che permette, oltre a monitorare il funzionamento e le performance di macchinari di produzione e sensori IoT, di integrare direttamente il dispositivo che genera l’aria compressa: il compressore.
In un’azienda cliente del settore del marmo, IDA ha permesso di analizzare in tempo reale i dati di utilizzo dell’aria compressa e di identificare delle anomalie di consumo. Oltre ai dati forniti dal compressore, che si riferiscono ai consumi totali dello stabilimento, sono stati installati sensori IoT a bordo macchina per misurare i consumi d’aria compressa in ogni singolo punto di utilizzo.
Dall’analisi di questi dati è emerso fin da subito che il consumo diurno d’aria compressa era pressoché identico a quello notturno, nonostante l’azienda non fosse operativa di notte. Un ulteriore aspetto di immediata rilevanza è stato il rilevamento di un consumo nullo di aria compressa durante i weekend e nel periodo estivo, poiché il compressore veniva spento per ridurre i consumi. Questa osservazione è stata successivamente verificata e confermata con il direttore di stabilimento.
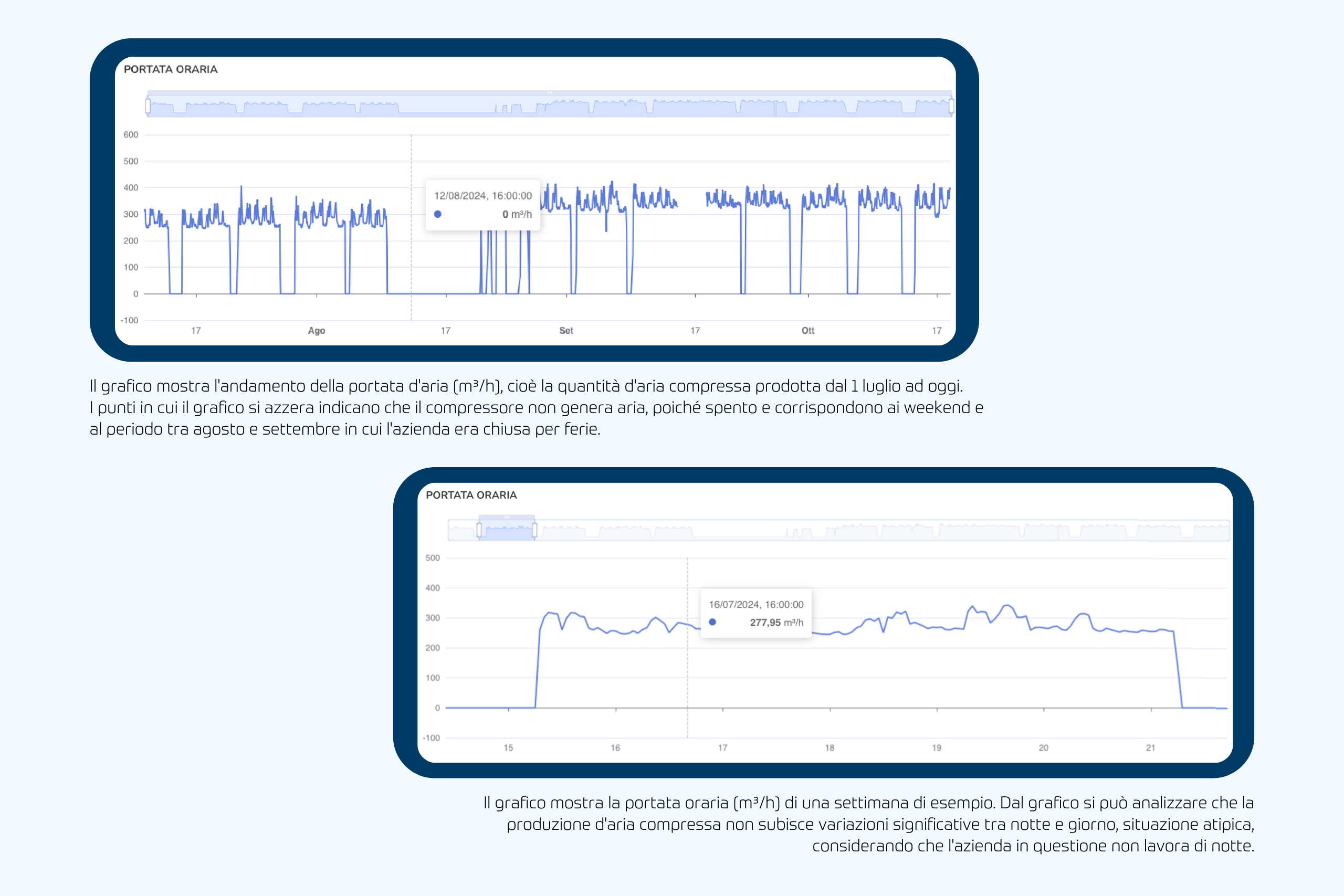
I dati raccolti
Stando ad alcuni studi di settore, una perdita d’aria compressa dovuta ad un foro di 3mm di diametro equivale a circa €2.800 di consumi di energia elettrica all’anno per un sistema a 6 bar, €7.760 per un sistema a 12 bar. Inoltre, il costo di energia elettrica stimato per generare 1m³ d’aria compressa oscilla tra i 0,015€ e i 0,030€* (supponendo il prezzo dell’elettricità: 0,10 €/kWh). Questi valori, seppur a primo sguardo possono apparire contenuti, nell’arco dell’anno comportano consumi e costi notevoli, soprattutto nel settore manifatturiero dove l’aria compressa è largamente utilizzata nelle lavorazioni e come alimentazione di molti macchinari. Inoltre, questi valori non tengono in considerazione i costi dovuti alla manutenzione del compressore.
Nello specifico, per il cliente in questione, Maxfone ha connesso direttamente il compressore, da cui è stato possibile estrapolare i dati di utilizzo e performance. Infatti, essendo dotati di connettività, questi macchinari sono facilmente accessibili e sono in grado di mostrare i consumi totali dell’impianto produttivo che alimentano.
Attraverso l’analisi dei dati con l’applicazione IDA, i nostri esperti hanno rilevato anomalie nelle misurazioni, specialmente durante le ore notturne, quando l’azienda è chiusa e l’impianto produttivo è inattivo. Durante questi periodo, dai grafici è risultato che il compressore produceva in media circa 250m³ di aria compressa all’ora, con un costo stimato di circa 6€ l’ora in termini di consumo elettrico. Su base mensile, questo si traduce in una spesa di circa 4.400€ e, su base annua, di 53.000€, (applicando una stima di costi di produzione di 0,0245€/m³).
Questo consumo si manteneva costante di notte, mentre di giorno cresceva a poco più di 320m³ d’aria l’ora, incremento dovuto al fatto che le macchine, al netto delle perdite, richiedevano più aria compressa per il loro funzionamento. Ciò significa che il fabbisogno reale dell’azienda in orari di piena produttività oscilla tra gli 80m³ e i 100m³ l’ora, circa il 25-30% del consumo generato e misurato dal compressore.
Dopo un’attenta analisi in stabilimento, si è individuata la fonte primaria del problema: alcuni sistemi di sollevamento, utilizzati per la movimentazione delle lastre di marmo tramite ventose a vuoto alimentate ad aria compressa, venivano lasciati aperti dagli operatori, indipendentemente dall’effettivo utilizzo. Inoltre, misurando il consumo d’aria delle singole macchine, si sono riscontrate delle perdite consistenti anche da queste, dovute principalmente all’usura dell’impianto e delle macchine stesse.
L’analisi dei dati e l’uso di uno strumento digitale come IDA hanno rivelato chiaramente la presenza di un problema significativo, responsabile di inefficienze, cali di produttività e costi nascosti, facilmente risolvibili. Con IDA è emerso che l’azienda può operare in modo ottimizzato utilizzando solo 80-100 m³ di aria compressa all’ora, riducendo così i costi di produzione dell’aria compressa fino all’70%.
Questo risparmio annuo di circa 53.000 € non include i costi aggiuntivi legati alla manutenzione: se il compressore lavorasse meno, richiederebbe meno interventi, si usurerebbe più lentamente e durerebbe di più, mentre l’uso eccessivo ne accelera l’invecchiamento e aumenta la necessità di manutenzione.
La soluzione sviluppata da Maxfone si è dimostrata perfettamente in linea con le esigenze dell’industria, che richiede soluzioni rapide, mirate ed estremamente efficaci. L’intervento infatti si è dimostrato vincente non solo per l’ottimizzazione di processo ottenuto, ma anche per la rapidità con cui è stato identificato il problema: grazie ai sensori IoT installati e alla connessione del compressore, sono bastate un paio di settimane per individuare e risolvere l’anomalia.
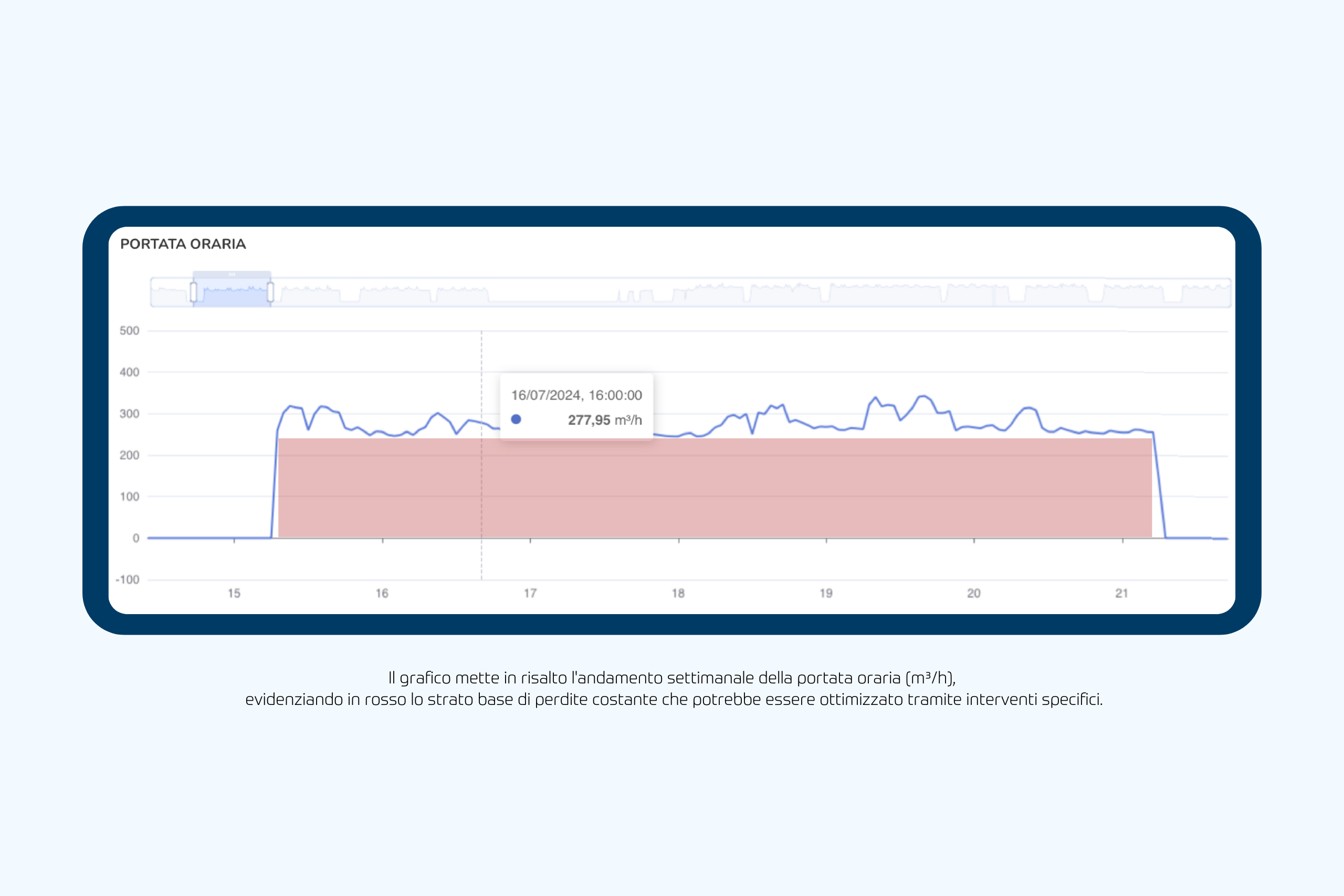
Il contributo di IDA
L’impatto significativo del consumo energetico sulla bolletta mensile ha spinto l’azienda a supervisionare con maggiore attenzione lo spegnimento dei sollevatori. Inoltre, sta valutando l’installazione di elettrovalvole automatizzate, controllate tramite IDA, per minimizzare perdite e consumi anomali, attivando le linee d’aria solo quando i macchinari sono effettivamente in funzione.
In termini di efficienza aziendale, IDA permette non solo di digitalizzare le macchine, fornendo visibilità sulle performance produttive dell’impianto, ma anche di identificare inefficienze che contribuiscono significativamente all’impatto ambientale e ai costi aziendali.
Il punto di forza di IDA è la praticità con cui fornisce dati evidenti alle aziende, garantendo loro la possibilità di controllare in modo semplice cosa succede a livello produttivo, ottimizzando i processi e arrivando a un concreto efficientamento dei processi.
Avere tutti i dati raccolti su un’unica piattaforma consente di quantificare il consumo energetico legato a una lavorazione. Ecco che i sensori collegati alle macchine possono fornire ulteriori informazioni utili a conoscere il reale stato di salute delle macchine e a individuare in anticipo eventuali malfunzionamenti. È così che nascono le manutenzioni predittive e prescrittive, punto di forza per tutte le aziende di qualunque settore.
Creare un’alleanza con IDA significa avere il pieno controllo sui propri processi produttivi. E, parafrasando un famoso motto, il controllo è la commodity che serve alla tua azienda per aumentare la sua potenza.
*Fonte1: CompAir: Evitare le perdite d’aria